Tankers away! Why invest in sludge dewatering equipment?
Are you still removing quantities of liquid sludge off-site for treatment and disposal? Here’s why the financial and environmental costs of tankering just aren’t stacking up anymore - and why investing in sludge dewatering equipment could be the answer.
What is is sludge worth?
Liquid sludge can be up to 75% water, but its solid contents can be rich in organic materials ripe for conversion into biofuel or fertiliser through the process of Anaerobic Digestion (AD). In fact, AD plants are becoming an important part of the commercial waste disposal eco-system, with plant owners prepared to pay for quality, dewatered sludge ‘cake’ to convert into bioenergy.
Right now, though, many food and beverage manufacturers producing liquid sludge suitable for dewatering and reuse are simply paying for it to be tankered off-site.
In doing so, they are not only ignoring opportunities to cut their carbon footprint. But they are forgoing potential participation in a UK waste-to-energy market that has risen to around £2,300 million p.a. in the last few years. (source Global Data).
Is it worth dewatering your own sludge?
The decision to dewater sludge on-site and sell the remaining ‘cake’ into the circular economy can be a win/win for the planet and your commercial bottom line.
But winning the internal argument for investment and committing to an on-site sludge dewatering solution can seem a daunting prospect.
To help with these sticking points, this blog post will explore:
- The business case for change
- The visible and invisible costs of off-site liquid sludge disposal
- The on-site dewatering options your business should consider
Calculating the cost of liquid sludge removal
What’s the cost of sludge tankering?
It’s easy to see the spiralling costs of third-party effluent disposal as you look at your annual tankering bill. The cost of diesel has more than doubled in the last 20 years, with wild fluctuations in the last 12 months thanks to the war in Ukraine. Diesel costs are outstripping inflation and impacting businesses' bottom line. But there’s also the spiralling environmental and social cost of tankering to think about.
What’s the carbon footprint of your tankering activity
Here’s one way to calculate the amount of carbon your sludge tankering process is pumping into the atmosphere. Taking into account the whole carbon footprint of generating and burning each gallon of diesel you use, the 8 Billion Trees project reckons median HGV emissions now equal 1,700 grammes of CO2 per mile. So, once you know your annual tankering mileage, you can calculate your total carbon footprint in metric tonnes.
What’s the ‘social cost’ of your carbon footprint?
Each metric tonne of carbon emitted represents a financial cost to the planet and its people through climate change and pollution. Researchers from the London School of Economics have estimated the cost of this damage to infrastructure, agricultural production and public health could be as much as £175 per tonne of carbon emitted.
What happens to your waste after it’s tankered away?
If you are trying to work out the total carbon footprint of your liquid sludge management, you should also consider what happens throughout your supply chain. But the problem is when you tanker away your waste with a third party, you often have little visibility and control over what happens to it next.
Mixed with other producers’ waste, your sludge may be subject to unnecessary or excessive chemical treatment before disposal. It may be incinerated or dumped in landfill. All of which can add to its total carbon footprint and further pollute our ecosystems in ways that are increasingly unsustainable.
“Every year, landfills in the UK release over 14 million metric tonnes of carbon dioxide into the atmosphere. At the current landfilling rate, the UK will also simply run out of landfilling space by 2035.”
Source: Sumitomo
How can you achieve carbon neutrality in your sludge treatment?
But there is a solution to this loss of control.
If manufacturers can treat their own wastewater and dewater their own sludge for disposal or sale at AD plants, they can start to measure their own carbon footprint in a meaningful way.
Here’s how dewatering on site can help you understand and unlock your route to ‘carbon neutral’.
- Reduce the amount of tankering traffic going to and from sites
- Reduce energy consumption within your site
- Capture and reuse treated water to power your plant
- Contribute to the circular economy through cake sales to AD plants
All while creating new cost efficiencies and revenue streams for your business.
What are the available solutions for dewatering on-site?
With the right machinery and use of chemical packages, manufacturers can thicken and dewater sludge on site, ready for transportation to AD plants. And if the water is treated successfully, it can even be funnelled back into your plant to reduce your overall water and energy consumption.
Here’s a brief guide to some of the dewatering options available:
Belt Press Dewatering
The belt press is a widely used dewatering technology, especially for large-scale operations. One of its primary advantages is its continuous operation, allowing for high throughput rates. This makes it suitable for handling large volumes of sludge. Additionally, belt presses tend to have lower power consumption compared to centrifuges, leading to potential energy savings. However, on the downside, belt presses often require a larger footprint and introduce most dust into the local atmosphere, making them less ideal for facilities with space constraints. They also necessitate regular maintenance and can be prone to clogging, which might increase operational costs over time.
Centrifuge Dewatering
Centrifuges are known for their efficiency in separating solids from liquids. They offer high solid capture rates and can achieve higher dryness levels compared to belt presses. This means that the resulting sludge cake is drier and can lead to cost savings in disposal. Centrifuges are also compact, requiring less space than belt presses. However, they come with their own set of challenges. Centrifuges typically consume more power, leading to higher energy costs. They also have more moving parts, which can increase maintenance requirements and costs. Additionally, the initial investment for a centrifuge can be higher than other dewatering options.
Screw Press Dewatering
Screw presses, or volute dewatering screws, are gaining popularity due to their simplicity and efficiency.
A screw press consists of a cylindrical screen and a rotating screw that pushes sludge through the screen, separating the liquid from the solids. The dewatered solids are then collected at the end of the press, while the separated liquid is discharged through the screen.
Screw presses offer several advantages over other dewatering options. They can be built off-site and easily installed, connected and commissioned by engineers wherever required.
Additionally, they require very little maintenance. This makes them a popular choice for industrial clients who have limited space available but wish to maximise control over their treatment and disposal process. The latest technology in this space is overcoming many familiar objections to undertaking on-site sludge treatment.
As Envirotech magazine comments:
“A Screw Press can significantly reduce sludge volume. Low energy, low noise and fully automated, it runs a continuous process, with a unique self-cleaning mechanism that prevents clogging.”
For manufacturers looking to start processing their sludge to sell on to AD plants, it’s an economical way to produce dried cake of sufficient quality for re-sale that’s easy to store and easy to transport.
It’s also worth mentioning, that for companies who are exploring ways to become more sustainable, but are wary of committing to big Capex products, a trial of a screw press solution can quickly demonstrate the business case for dewatering with minimum operational disruption.
Turning around tankering costs through smarter sludge treatment
In 2021, WCSEE met a client who was producing around 200 tankers of liquid sludge every year, transporting them via road to their waste transfer site.
Based on site trials and laboratory tests, we calculated that moving to the Dewatering Screw system would reduce the volume of sludge they produced annually by 75-80%.
Through on-site dewatering, the client reduced their tankering requirements by 150 trips every year, bringing a huge 25.5 metric tons reduction in CO2 emissions through HGV trips alone.
Conclusion
Dewatering with a screw press solution offers industrial clients a low-energy, low-maintenance way to cut their carbon footprint and join the circular economy. It cuts out the need to transport large volumes of unprocessed waste. It can save money and create new revenue streams with a portable and ready-to-use product for growing markets.
- Reduces overall running costs for effluent disposal.
- Can open up resale opportunities in the bioenergy and fertiliser markets.
- Reduces transport, fuel and disposal costs by reducing tankering.
- Reduces exhaust emissions, carbon footprints and congestion.
Importantly, it can also become part of the sustainability story that speaks to your brand's long term environmental commitments.
Topics: Wastewater Treatment
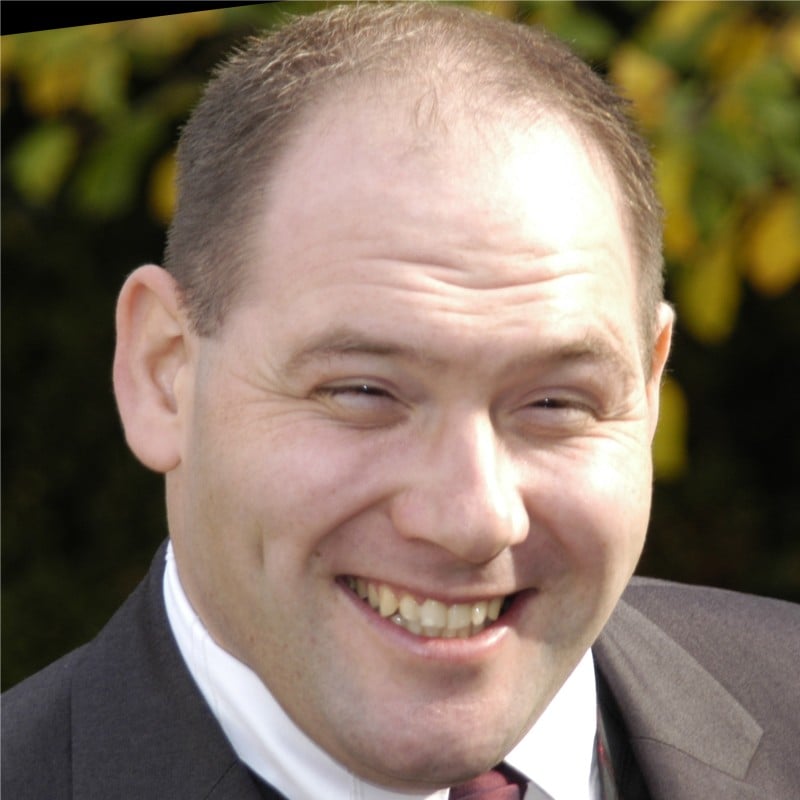
Written by Pete Cranney
Pete Cranney has worked for Atana (now part of WCSEE) since 2003 and has experience across every part of the business. Specialising in food & drink manufacturing, Pete can recommend the most practical and cost-effective treatment processes, designing onsite solutions that achieve strict discharge consents. In previous roles, Pete has managed full treatment plants for clients such as PepsiCo and Kraft Heinz. He has also led on laboratory testing of client samples. In process design, Pete provides clients with the most effective blends of chemical and mechanical treatments to ensure their sites offer full environmental protection 24/7.