Purification of water and water safety in Food Processing
Pure water is essential in healthy fruit and vegetable growth, but are producers’ water supplies pure enough to deliver cost and efficiency savings that will help them thrive? Tim Gaston, WCS Group’s Head of Engineering, shares insights around water purification and disinfection.
From field or polytunnel to plate or bowl, water plays a vital role at various stages in the production of fresh produce. Irrigation, washing and handling within production facilities relies on a consistent supply of pure water to stimulate healthy growth and deliver clean and saleable produce to the end customer.
With various methods for indoor and outdoor growth, as well as emerging techniques such as hydroponics which substitutes soil with water-based solutions for better results, fruit and vegetable producers are tasked with balancing product quality with speed to market in order to satisfy growing consumer demand.
But without a consistent level of water purity, producers can experience a number of challenges. For example, Pythium can thrive in poorly treated water which can lead to dead roots, stunted growth, wilting and rot, not to mention ulcers when passed on to the consumer through poor quality produce.
By following these top tips when assessing your existing water purification system or considering the implementation of a new system, you can ensure your chosen solution is delivering the best possible service for your business:
1. Switch up your purification process
Process water in irrigation systems typically relies on chlorination to tackle the above challenges, yet recent developments in chlorine dioxide (ClO2) dosing make it simpler and easier to overcome the challenges.
Compared to chlorination, ClO2 results in a higher kill rate of waterborne organisms and removes biofilm. In turn, this results in fewer blocked drippers and the reduction of fungus in the water system. With these challenges diminished, hydroponic producers can significantly reduce produce wastage, creating a larger yield.
2. Invest in sequential batching
While two-pack ClO₂ generators are widely available, a generator fitted with a sequential batching system overcome various drawbacks typically associated with two-pack design. These sequential systems are particularly effective against Biofouling (Sessile Bacteria) and Legionella, Pseudomonas and Cryptosporidium among many other pathogenic microorganisms. (Planktonic Bacteria).
As the safest, purest and most stable method of producing ClO2 onsite, these systems (and Catalytic Technology options) optimise the conversion reaction to ensure that the ClO2 being produced is at its purest. These systems require lower chemical concentrations making them easier to dose, with some models achieving over 90 percent conversion efficiency.
3. Choose a purification system that uses smart software
The chosen system should include built-in service software which stores service and treatment information. Having this repository of data is beneficial when it comes to optimising system performance. Service engineers can easily access vital data that will enable them to track the system’s historic performance and adjust the system’s performance for optimal future operation.
Software-operated systems saves time, removing paper-based logging of operations, where mistakes can easily occur through human error. This automated logging removes a menial task for personnel, enabling them to get on with more important and fulfilling tasks.
For guidance and to understand options and the differences between water purification technology options, download our Water safety, purification of water, secondary disinfection eBook here.
4. Ensure your purification system is WRAS compliant
In the UK, WRAS (Water Regulations Advisory Scheme) compliance is a requirement for many systems that carry or receive water from the public mains water supply. Any fitting that will carry or receive water from the local water authority’s mains water supply must comply. This requires that the water fitting must not cause waste, misuse, undue consumption or contamination of the water supply and must be of ‘an appropriate quality and standard’.
5. Consider water reuse
Once it has served its purpose, waste water is traditionally sent to the drain. However, a percentage of this water can be re-used in the process, saving the producer energy expenditure savings from five percent upwards. This can all be achieved through the implementation of a turn-key, pre-treatment plant which will also reduce the cost of draining waste water away.
By channelling drain-away water through a specific cycle of pre-treatment and treatment cycles, it can be reused a finite number of times, increasing sustainability credentials for fruit and vegetable producers alongside those cost savings.
Implementing smarter water management practices such as ClO2 dosing and water recycling will enable fruit and vegetable growers to reduce their cost of operation, achieve greater sustainability targets and, most importantly, produce higher, healthier yields.
Further reading: Water Safety eBook “Water safety, purification of water, secondary disinfection”
Topics: Water Treatment & Hygiene
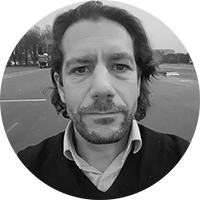
Written by Tim Gaston
Tim heads up the National Engineering Division with over 17 years’ experience in water treatment engineering, engineering management and product development. Holding a Degree in Biology and Ecology, Tim started work in the Water Treatment industry as a Sales and Service Engineer.