7 tips for successful pre-commission cleaning of pipes and pipework
Pre-commission cleaning of pipework can ensure the performance and longevity of open and closed water systems. But, when is it applicable and what are the requirements, benefits and possible pitfalls of the procedure?
When is pre-commission cleaning required?
Chemical cleaning is not compulsory for all systems, although the majority of systems will benefit from some form of chemical cleaning to supplement clean water flushing
But pre-commission cleaning is a standard requirement for new closed water installations under the guidelines published by BSRIA.
The two guidance documents relating to pre-commissioning cleaning published by the body are:
BSRIA BG29:2012 Pre-commission Cleaning of Closed Systems
Why do closed systems need special attention?
Newly fabricated and installed closed water systems can harbour mill scale, jointing compound and a catalogue of other debris associated with factories and building sites.
Systems that are not properly cleaned of these contaminants prior to use can be subject to the unwanted build-up of sludge and bacteria over time. This, in turn, can cause corrosion, blockages and biofouling leading to inefficiencies, leaks and other costly system failures.
Ineffective cleaning can cause suspended solids, biofilm, grease and oil to remain in your system, producing an immovable layer on the pipework. This will mean inhibitors will not reach the metal surface and, therefore, cannot prevent future corrosion.
Can you use the BSRIA guidelines for cleaning pre-existing systems?
In their guidance the BSRIA state the following:
“When cleaning existing systems, the history, pipework conditions and reasons for the flushing or cleaning need to be assessed to determine the likely outcome before works proceed. It is generally the case that parameters set out in BSRIA 29/2012 can be used as a target for water quality and that any deviation should be logical based upon the above assessment.”
So, what are our 7 tips for pre-commission cleaning of pipes and pipework?
1. Plan your pre-commission cleaning to address four main types of contaminants – these are the elements that, if unaddressed, can cause poor performance, system failures and costly maintenance further down the line,
- Foreign body and installation debris
- Scale
- Corrosion products
- Biological fouling
2. The type of pre-commission cleaning required will be influenced by:
- The size of the system and the kind of debris likely to be present
- Whether the system is open, closed or partially open. As mentioned above - very specific chemical treatment is required when existing contaminants could become trapped and allowed to multiply unchecked.
- System materials and construction. Different materials such as stainless steel, copper and plastic have different tolerances, susceptibilities and cleaning requirements. For example, the new BSRIA guidelines stipulate the specific cleaning precautions necessary for thin-walled carbon steel pipes.
- System complexity. Equipment such as chillers, small-bore control and regulating valves, low water content heat exchangers and flow rate monitoring can all be prone to blockage if dirt is allowed to accumulate in the system. At the same time, systems that use glycol-based anti-freeze are particularly sensitive to contamination, as glycol can actually be a nutrient for bacteria if not maintained at the correct levels.
- If a system has been added to or extended over time. It should be noted that cleaning and treatment of existing systems (or new systems incorporating old pipework) should only be undertaken with advice from a chemical cleaning or water treatment specialist.
- The length of construction period which may have increased the likelihood of damp ingress, biofilm build-up and corrosion.
- System pressure, flow rates and operating temperatures. These varying factors can all dictate the type of cleaning treatment required and the frequency with which follow up activity has to be completed after the initial clean has been done.
3. Plan for the nine possible stages of a system clean, but follow advice to determine what your system requires :
- Static flushing
- Dynamic flushing
- Degreasing
- Biocide wash for systems at risk from bacteria
- Removal of surface oxides for systems with mild steel components
- Effluent disposal or final flushing
- Neutralisation for inhibited acid cleans
- Passivation
- The introduction of corrosion inhibitor and biocidal dosing
4. Understand the overall success of a system clean is dependent on the thoroughness of each recommended stage of the clean. Ensure each one is conducted for the required duration and at the appropriate intervals for best results.
5. Test for success. To be sure your clean has been successful, test for bacteria level. Take water samples from representative system extremities and low points. Check for and maintain system pressure and do not contaminate sample results by topping up or replacing water loss. Don’t forget, the introduction of a body of fresh water could re-introduce contamination
6. Remember, pre-commission cleaning can fail if:
- There has been an excessive period of stagnation before commissioning
- An engineer has failed to recognise system characteristics when selecting a suitable water treatment
- There has been a failure to correct pressurisation issues during commissioning leading to oxygen ingress
- There has been a failure to maintain water treatment between pre-commission cleaning and handover
- There has been excessive draining and refilling leading to loss of treatment
- There has been a failure to act on water quality results
7. Throughout the process you need to ensure your system is continuously monitored so that changes can be tracked, recorded and the appropriate action taken to rectify issues. Use Hevasure to independently monitor conditions before, during and after and cleaning procedure to ensure that oxygen levels are low and corrosion is under control.
Conclusion
There is no ‘one size fits all’ method for pre-commission cleaning. Every water system is different in its setting and design, as well as its intended use. Take advice on the best approach for your specific system and follow the recommendations carefully to ensure its future optimal performance and longevity.
Topics: Water Treatment & Hygiene
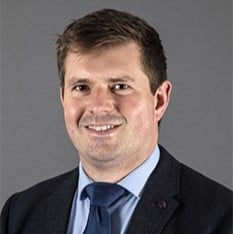
Written by Jon Greaves
Jon has progressively worked through operational roles, account management, technical management, and senior management roles over the last 16 years within one of the group companies before moving into the role of Water and Air Managing Director. Jon has experience across multiple sectors of water and air compliance, including district energy networks; data centres; healthcare; food and beverage and facilities management. Jon acted as a corresponding steering committee member on CIBSE CP1 – Heat Networks Code of Practice for the UK released in 2020.