Closed Loop Water Treatment Chemicals
Closed loop water systems are used in a variety of industrial processes – perhaps the most common is in heating systems. They have a number of advantages over open water systems, including greater efficiency and lower maintenance requirements but it would be wrong to think of them as maintenance-free.
Although by their very nature they are not susceptible to outside contaminants or water loss, they can still be affected during routine maintenance and refurbishment work by adverse factors such as corrosion and microbiological contamination potentially entering the system via oxygenated make up water, sometimes from less than ideal sources.
With modern, energy-efficient systems being installed with low-velocity water flow and leaner materials – it is more important than ever to maintain the quality of the water and the integrity of the infrastructure that make up closed systems.
The importance of control and management
To ensure closed circuit heating and cooling systems are well maintained and operate efficiently, water chemistry and conditions need to be controlled and managed precisely.
Because a closed water system is usually impossible to view from the inside, monitoring in some form is essential to understanding the state of a closed water system. The information produced by an analysis of the water will help you plan any maintenance required. Monitoring can be completed by physically removing and testing representative samples of the water, or inline and online monitoring systems are now becoming more prevalent.
There are two elements to maintaining an efficient closed loop water system
- The integrity of the system
- The water chemistry
Checking System Integrity
A thorough visual inspection of the system should be carried out to check for leaks or damage. Any suspected issues should be addressed before they become critical. Measuring water flow and pressure for fluctuations will also be useful in determining if there are any issues with the physical system.
Water chemistry is a dominant factor
Any deterioration in the physical system, however, is most likely to be due to a change in the water chemistry. A lowered pH value could indicate bacterial growth or a leak. Bacteria can create biofilm which can coat surfaces making them less efficient. Contaminants can result from unseen corrosion.
Because problems with a closed system can be difficult to spot until the system shows signs of failure, preventative chemical treatments are critical to maintaining efficiency and longevity.
Water Analysis
Immediately after the handover from pre-commission cleaning is the ideal time to undertake a BSRIA Closed System Water Analysis – BG 50/2015.
A BSRIA analysis is a comprehensive set of tests that cover a full range of chemistry and micro-analysis.
A Standard closed system analysis would typically look at
- pH
- Alkalinity
- TDS
- Nitrite
- Tannin
- Molybdate
- Phosphate
- Glycol % (if type known)
- Iron
- Aluminium
- Copper
Performing analysis regularly is important to keep on top of your closed system water treatment levels as poor management can lead to scale & corrosion issues, reduced efficiency and even damage to critical systems.
Closed System Scale and Corrosion Inhibitors
Several factors can cause corrosion:
- Surface Condition – dirt & contamination may encourage localised corrosion
- Bacteria – the risk of corrosion from aerobic & anaerobic bacteria
- pH – pH below 7 may see rapid corrosion (Aluminium corrosion can occur at high pH so treatment program should be limited to pH of 8.5)
- Dissolved Oxygen – most important factor to govern corrosion
- Dissolved Carbon Dioxide – can cause a reduction in pH
- Galvanic – Aluminium & Copper corrosion due to ‘electrochemical potential difference’
- Temperature – higher temperatures tend to increase rates of corrosion
- TDS (Total Dissolved Solids) – high conductivity aids certain corrosion processes
- Chloride attack – high levels can interfere with the development of protective oxide films on surfaces
- Sulphates – high levels can increase corrosion, additionally, sulphate ions may be consumed by SRBs (Sulphite Reducing Bacteria) to cause pitting
- Flow Velocity – turbulent erosion on softer metals (low risk)
- Stress – stress-corrosion cracking
Closed System Biocides
Untreated closed water systems can become an environment for a variety of undesirable microbes including nitrifying and sulphate reducing bacteria, pseudomonas and more. Such microbes can cause corrosion and fouling.
Once a closed water system has a problem it is time-consuming and costly to clean up – it is far more economical to take action to prevent any problems from manifesting.
To do this, closed system biocides should be deployed to prevent slime growth in any system operating below 80° C. Even systems operating at a higher temperature would benefit from treatment and any system being shut down for any length of time should also be treated to protect the system whilst it is inactive.
Bacteria levels within the closed system should be tested for regularly as part of the PPM regime. Any signs of growth should trigger an investigation into the causes and potentially a more aggressive treatment routine.
If there are still problems, the biocide should be tested to ascertain whether a different biocide should be applied to improve the situation.
Pre-Commission Cleaning Products
Any new system should be thoroughly flushed through and cleaned with specialist cleaning products before it is commissioned, to ensure the best possible performance and to help reduce any initial problems.
System Flush Products
Where any system is suspected to suffer from contaminants such as debris from repairs, long term build-up, waste from manufacturing processes or unexpected break downs, one course of action may be to wash the system through using chemical cleaning and high-speed flushing. However this should not be completed until there is an excellent understanding of the route cause of any issue.
Conclusion
Closed water systems are generally easier to maintain, as the dosage levels of the appropriate corrosion and biocide inhibiting chemicals can be considerably higher than those in an open water system. But without a schedule of testing and analysis – in partnership with a chemical treatment programme, even a closed water system will suffer the problems of corrosion, scale and microbial build-up.
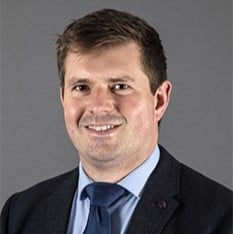
Written by Jon Greaves
Jon has progressively worked through operational roles, account management, technical management, and senior management roles over the last 16 years within one of the group companies before moving into the role of Water and Air Managing Director. Jon has experience across multiple sectors of water and air compliance, including district energy networks; data centres; healthcare; food and beverage and facilities management. Jon acted as a corresponding steering committee member on CIBSE CP1 – Heat Networks Code of Practice for the UK released in 2020.