Biocides and Closed-Circuit Systems: What you need to know
Biocides are used within closed circuit heating and chilled systems to control microbial growth as part of a water treatment regime. They break down destructive debris and settled solids caused by micro-organisms. Dosing your system with the correct biocidal treatment is key to minimising microbially induced corrosion and associated, additional blockages. They will optimise system performance and reduce the potential cost and scale of future maintenance work.

Micro-organisms found in closed-circuit systems can lead to the build-up of biofilm in pipework and on heat exchanger surfaces. This can cause flow restrictions and under deposit corrosion.
To treat a system effectively, you should monitor bacteriological levels on a regular basis and if necessary dose an effective biocide to keep the system running effectively.
Here’s what else you need to know about maintaining an effective biocide regime:
1. Temperature
Biocides are highly recommended for closed-circuit heating and chiller systems operating below 60c. But they are also necessary if there are sections in the system that don’t reach this temperature consistently (i.e. seasonal systems).
BSRIA BG 50 suggests a minimum circulation period of one hour per day, even for those systems that are only used for part of the year.
2. New Closed Circuit System Installations
When installing new systems it is vital to ensure that the system is clean and that the pre-commission cleaning process includes an appropriate biocide as part of a biocidal flushing process. This process is described in BSRIA BG29/ 2020.
3. Ensure the correct concentration
You should ensure that a suitable closed-circuit biocide and closed-circuit inhibitor are present in your system at the correct concentration during:
- First fill
- Pressure testing
- At regular intervals throughout its lifecycle
4. Closed system chemistry testing and microbiological monitoring
rChemistry testing and microbiological monitoring is an essential part of an ongoing maintenance regime.
You should measure biocide effectiveness by testing the system for microbiolocial activity on a regular basis. If your test result indicates increased microbiological growth and loss of bacteria control, you should review previous results and consider dosing to bring the system back under appropriate control
With problematic sites - for example, one that experiences a frequent loss of pressure or repeated blowdowns - you should consider online constant monitoring, (such as Hevasure and/or full laboratory water analysis) to determine any underlying system issues. Shock dosing of a biocide in response to high bacterial numbers should ensure that control of microbial numbers is achieved, but that's not the only answer. It’s important to understand why, if you are to stop the bacteria coming back.
5. Biocide sensitivity analysis
It is always possible that resistance to a particular biocide may develop over time. This can mean a change of dosing regime is required. With a particularly problematic system, it may be necessary to carry out biocide sensitivity analysis to discover which biocide will be most effective.
6. Biodispersants
It is easier and more cost-effective to maintain microbiological control than to clean a badly fouled system containing significant biofilm (see BSRIA29)
Where a build-up of biofilm is present together with a high level of bacteria, dosing an effective biocide with a compatible biodispersant may be needed. If a system has strainers/filters dispersed throughout the system, these will need to be inspected and cleaned frequently after dosing to remove dislodged biofilm. But if the system contains small bore pipework and no strainers or filters, it may become prone to blockages. Addition of a biodispersant is therefore not the right solution for all systems.
7. Glycol
For chiller systems containing glycol, the levels must be maintained at optimal concentrations, not only to protect the system from frost damage, but at 25% glycol can help to prevent bacterial growth. A dose of around 25% ensures systems are biostatic and inhibits the growth of bacteria. Below this level, glycol can actually be a nutrient for bacteria.
8. Risk Assess
It almost goes without saying that biocidal products must be handled with caution. Operatives should carry out a risk assessment and if required, wear the right personal protective equipment (PPE) at all times when working with them. The Safety Data Sheet (SDS) of each biocide must be consulted before use.
The presence of damaging bacteria in closed heating and chilled systems can cause a number of serious problems listed above. What’s more, a system that is not frequently tested and treated for microbial growth, can consistently underperform and affect the data being extracted from it. This in turn, can lead to poorly configured systems that can further exacerbate and accelerate their deterioration.
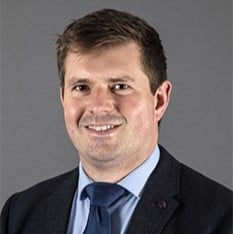
Written by Jon Greaves
Jon has progressively worked through operational roles, account management, technical management, and senior management roles over the last 16 years within one of the group companies before moving into the role of Water and Air Managing Director. Jon has experience across multiple sectors of water and air compliance, including district energy networks; data centres; healthcare; food and beverage and facilities management. Jon acted as a corresponding steering committee member on CIBSE CP1 – Heat Networks Code of Practice for the UK released in 2020.