10 of the best types of wastewater equipment for industry
Trade effluent is wastewater produced by any business as part of its commercial activity. In England and Wales, companies must adhere to strict regulations established in Section 118 of the Water Industry Act 1991 and have the sewerage company's consent before discharging trade effluent into public sewers.
Sewage companies require businesses producing trade effluent to regularly report to them and keep records about their wastewater treatment. Also, they often stipulate conditions about the effluent's quantity, quality, temperature, acidity, and alkalinity.
What can you do with trade effluent?
There are three ways a business can treat its effluent.
- Discharge to surface waters: Your business must have approved consent to discharge.
- Discharge to sewers: Your business can discharge its effluent into local sewers; however, you must adhere to pre-set limits or receive a fine.
- Treat the wastewater yourselves: You ensure your wastewater is treated effectively so it can be discharged compliantly or reused.
While you are allowed to discharge your trade effluent, treating it yourself will help your business in three critical ways:
- Prevent fines from the sewage company
- Reduce your business’s impact on the environment
- Improve your brand image and reputation
Here are ten of the best types of equipment your business can use as part of its wastewater treatment process.
1. Screw Press
Sludge dewatering equipment is made of corrosion-resistant materials and is one of the most effective methods to remove or treat sludge in water treatment. Using a self-cleaning moving ring mechanism, it prevents clogging that blocks the discharge of filtered liquid.
The Dewatering Screw Press runs continuously and dewaters sludge by up to 85% of moisture content. It offers both sludge thickening and dewatering for industrial wastewater applications. It is suitable for industrial, primary, and secondary treatment sludges, aerobic and anaerobic biosolids, and oily sludges.
The Screw Press is easy to operate and maintain, so it has low labour costs. It also has many other benefits, including the following:
- Runs automatically 24 hours on-site without a machinist
- Daily maintenance is minimal and will not require any skilled labour
- No thickening or storage tanks needed
- A unique self-cleaning mechanism prevents the filter mesh from clogging
- All-in-one design and easy to install
- High resistance to oily sludge
- Power-saving
- Water-saving
2. Dissolved Air Flotation (DAF)
Dissolved Air Flotation (DAF) systems remove suspended solids, fats, oils, and greases through a process of dissolving air into water under pressure.
First, the wastewater enters the DAF system through a header box, which, to optimise treatment, has many injection points, a highly saturated pressurised stream of air, DAF effluent, and flocculant. The header box distributes the water across the length of the vessel and reduces its velocity.
Second, the wastewater goes into the flotation zone, and microbubbles attach to the particles' surface, affecting the density. Consequently, suspended solids move to the surface of the DAF. They can then be skimmed off using a chain and removed into the sludge hopper.
Throughout the process inside the DAF, wastewater is continuously removed. And when it flows out of the DAF, the wastewater is finally discharged into an effluent chamber.
The ideal DAF achieves high rate removal efficiencies at a low operational cost with a smaller footprint and longer lifespan by employing such techniques as:
- Thickening sludge
- Removing sludge easily
- Maximising solids removal
- Lowering velocity and achieving better separation
- Achieving high removal efficiency and lower power requirement
- Extending retention time and producing a better effluent quality
3. Lamella Separators
Lamella Separators are designed to remove solids and particulates during wastewater treatment. If the water to be treated contains a high concentration of suspended solids, the Lamella Separator can remove them before the water enters the polishing stage.
Wastewater containing solids enters the Lamella Separator and flows between inclined flat plates. As the water passes through, the solids float to the top of the plates and then slide down them. Water free of solids flows out of the system, and the solids are collected in a sludge hopper.
The process is efficient and economical, and there are many advantages of choosing a Lamella Separator over another clarifying system. These include the following:
- High throughput with a minimal site footprint
- High solid-liquid separation efficiency
- Occupies 90% less space than traditional settling equipment
- Removes up to 95% turbidity, suspended solids, and associated pollutants
- Minimal operation and maintenance
- No moving parts within the clarifier, reducing the risk of downtime
- Option of an automatic sludge removal system to reduce operator time
- Low installation cost
- Quick set-up due to pre-configured weirs and fixed pipework
- Low-energy system that can work with or without chemicals
4. Screens
At wastewater screening plants, water is first screened to remove objects like plastic, paper, household waste, and metals. The process protects downstream equipment and pipes. Coarse screens remove large solids and debris from wastewater, and fine screens remove problematic material for downstream processes.
To remove bigger materials, large facilities generally use mechanically cleaned screening systems, which capture more objects and improve flow conditions. Conversely, smaller facilities use manually cleaned screening equipment, which does not need much equipment maintenance.
5. Submerged Aerated Filters (SAFs)
There are three types of SAF systems: combination systems, loop reactor systems, and compartmentalised systems. However, each system generally uses a settling tank to clarify the slough that enters via the water filtration system.
As part of the filtering process, biomass is grown on a bed of filter media. And a blower blows air to the bottom of this bed, supplying oxygen for the oxidation process. This air stream helps the effluent to mix effectively and disturbs any excess solids from the filter medium.
There are several benefits if biological treatment is used within the SAF, including an increased final effluent quality, total nitrogen removal, and total phosphorus removal.
There are a range of benefits of SAF systems, including the following:
- Minimal energy required
- Simple to operate
- Low maintenance costs
- Established and robust technology
- Low environmental impact
- Resilient to shock and toxic loads
- Cost-effective solution
- Computer software provides guaranteed effluent discharge quality
6. Sequencing batch reactors (SBR)
Sequencing batch reactors remove solids from wastewater over several cycles, thus reducing the level of organic matter in wastewater.
Wastewater passes through the first chamber of the reactor, where the solids are removed, before the water moves into the secondary chamber. The cycle is then repeated while oxygen is pumped into the tank, which cleans the water as microorganisms are activated, and the solids are removed. The sludge settles at the bottom of the tank, and it is then returned to the primary treatment chamber. The treated water moves to the top of the tank before being discharged.
The advantages of SBR include the following:
- No moving parts within the tank, which reduces maintenance costs and downtime
- Simplified process as all processes happen in one tank
- Effluent can be stored at peak periods and treated in smaller batches throughout the day
- Produces high effluent quality
7. Microscreens
Microscreens, also known as micro strainers, are used in primary and tertiary wastewater treatment as well as the treatment of stormwater. There are two types of micro screens: disc-and drum filters.
The process of micro-screening involves wastewater flowing into a drum that contains filter media. For solid waste removal, the most common type of filter is the drum filter, which physically blocks the particles. This build-up of particles impedes flow, causing a rise in the water level until a backwash process begins. The screening process continues while the solids are washed off the screens.
Microscreens can be used in both industrial and municipal wastewater treatment, helping operators to meet discharge requirements. They are energy efficient, even at peak design flow rates, and have several other benefits:
- Minimised maintenance costs
- Reduced handling of solids
- Increased efficiency
- Preventing damage to downstream processes
- Improving the efficiency of downstream processes
- Reducing contamination of watercourses
- Money savings due to reduced energy consumption and chemical use
- Separating effluents so materials can be recycled and reused—potentially to be converted to energy and sold
8. Ultrafiltration systems
Ultrafiltration (UF) systems use hollow membrane fibres to filter wastewater for coolant, metal hydroxides, bacteria, pathogens, metal hydroxides, dispersed materials, emulsified oils, and suspended solids. Pumps push the cleaned water through tiny pores that act as a physical barrier, letting only filtrates pass through. Next, particulates are removed from the filtered water before it enters the UF system using UF strainers.
UF plants efficiently treat wastewater and consistently produce outstanding results. After UF treatment, the water can either be delivered for direct public consumption or routed to a reverse osmosis system for additional purification.
Without adding chemicals, ultrafiltration systems can reduce the volume of oily water by up to 98%. They can also eliminate minute particulates, allowing the water and soap solution to be recycled and used again. Companies can also experience a decrease in wash water and detergent costs of up to 75% and a reduction in waste disposal costs of up to 90% when calculating heating and disposal charges. As a result, UF membrane technology is quickly replacing traditional filtration techniques as a preferred method.
UF systems are designed to reduce oily water volumes by as much as 98% without using chemical additives. These systems can also remove particulates and macromolecules, which allows the water to be recycled and reused.
Ultrafiltration systems are being chosen more frequently over standard filtration methods as they reduce wash water and detergent costs by up to 75% and waste disposal costs by up to 90%.
9. Oil separators
Contaminated water flows through a series of baffles and a porous media bed. The oil separator removes free-floating and mechanically dispersed tramp oils, inverted emulsions, bacteria, and slime as these are separated from the liquid.
When decontaminated, the water can be reused, and the contaminants are collected separately. The system uses gravity flow and coalescence to reduce tramp oils to less than 1%, and there is no need to use consumable products.
Tramp oil separators are simple, economical solutions to remove free-floating and mechanically dispersed tramp oil from individual machine sumps, central systems, and wash tanks. They are efficient solutions that rescue water detergents, heating, and disposal costs. They also reduce new fluid purchase costs by up to 75% and hazardous waste volumes by up to 90%. Return on investment can be in less than six months.
10. Reverse osmosis systems
Reverse osmosis (RO) technology removes contaminants (impurities and dissolved solids) from unfiltered water when forced through a semipermeable membrane at high pressure. The contaminants are left behind as the water passes through the RO membrane—the result is clean water or permeate.
The right RO system can remove up to 99.5% of impurities and the majority of colloidal and suspended matter, even from the most contaminated wastewater. Generally, RO systems are used in industrial applications.
A properly designed and operated RO system can remove up to 99.5% of incoming dissolved salts and impurities. RO technology is typically used for industrial treatment applications after wastewater has gone through either an ultrafiltration system or chemical treatment.
Topics: Wastewater Treatment
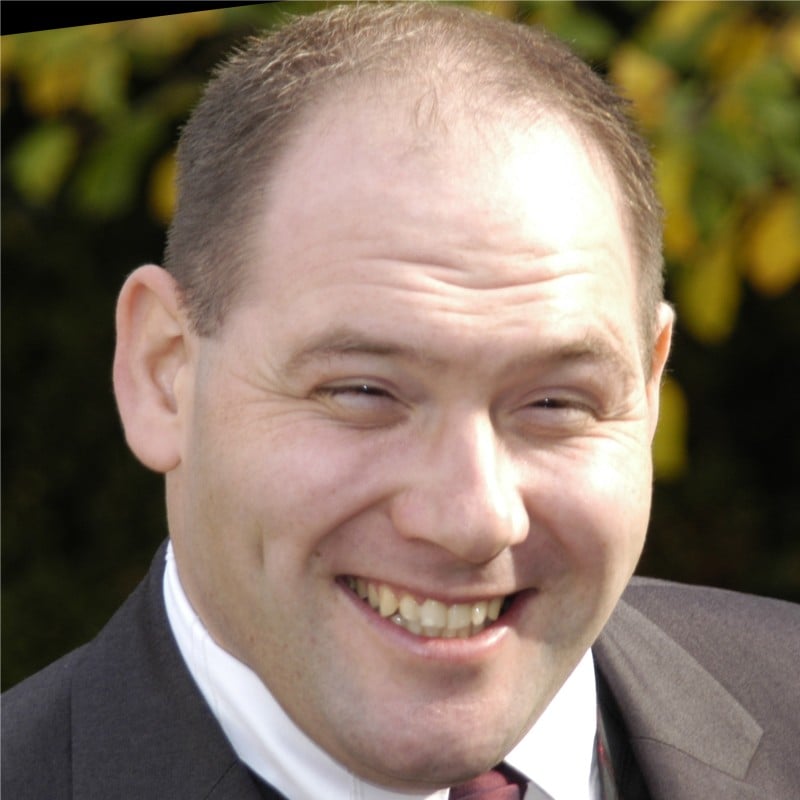
Written by Pete Cranney
Pete Cranney has worked for Atana (now part of WCSEE) since 2003 and has experience across every part of the business. Specialising in food & drink manufacturing, Pete can recommend the most practical and cost-effective treatment processes, designing onsite solutions that achieve strict discharge consents. In previous roles, Pete has managed full treatment plants for clients such as PepsiCo and Kraft Heinz. He has also led on laboratory testing of client samples. In process design, Pete provides clients with the most effective blends of chemical and mechanical treatments to ensure their sites offer full environmental protection 24/7.